Inventory Optimization & Supply Chain Management (Methods)
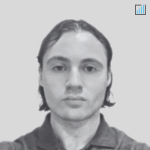
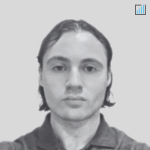
In the context of inventory optimization, supply chain management (SCM) refers to the oversight of materials, information, and finances as they move from supplier to manufacturer to wholesaler to retailer and finally to the consumer.
Effective SCM directly correlates with inventory optimization. It allows for reduced costs and improved efficiency.
This is important for traders and investors who analyze companies, as efficient SCM indicates strong operational processes.
This can lead to improved profitability and investment attractiveness.
Key Takeaways – Inventory Optimization & Supply Chain Management
- Effective inventory optimization and supply chain management signal a company’s operational health and market adaptability.
- Important for fundamental analysis of companies its relevant toward.
- Just in Time (JIT) is a strategy reducing inventory costs by receiving goods only when needed.
- Boost efficiency and reduces waste.
- Indicates a company’s operational proficiency.
- Economic Order Quantity (EOQ) calculates the optimal inventory order size to minimize costs.
- Helps in assessing a company’s inventory management and operational efficiency.
- Economic Production Quantity (EPQ) helps manufacturers determine ideal production quantities to minimize costs.
- Insights into production efficiency, cost management, and demand response.
- Economic Batch Quantity (EBQ) identifies optimal batch sizes to reduce setup and holding costs.
- Indicates a company’s ability to optimize production and inventory.
Let’s look at the different types of inventory optimization:
Just in Time (JIT)
Just in Time (JIT) is an inventory management strategy that involves receiving goods only as they are needed in the production process.
This approach is used to reduce inventory costs.
It can significantly increase a company’s efficiency and decrease waste.
For traders/investors, a company’s ability to effectively implement JIT can be a strong indicator of operational efficiency, cost management, and responsiveness to market changes.
Companies excelling in JIT may present lower operational risks and better profitability prospects.
Economic Order Quantity (EOQ)
Economic Order Quantity (EOQ) is a formula used to determine the optimal order quantity that minimizes the total cost of inventory, including ordering and holding costs.
Understanding a company’s EOQ helps traders/investors assess how well it manages inventory levels and controls related costs.
A well-optimized EOQ suggests a balance between inventory holding costs and order costs.
This can be an important factor in evaluating a company’s operational efficiency and cost-effectiveness.
Economic Production Quantity (EPQ)
Economic Production Quantity (EPQ) is a model used in inventory management to determine the ideal production quantity a company should produce to minimize the total costs of production, setup, and inventory holding.
EPQ is relevant for manufacturers, as it helps in balancing the production runs with holding costs.
For traders/investors, analyzing a company’s EPQ can provide insights into its:
- production efficiency
- cost management, and
- ability to respond to demand fluctuations without incurring excessive inventory costs
Economic Batch Quantity
Economic Batch Quantity (EBQ), also known as the lot-size model, is used to determine the optimal batch production quantity that minimizes the total cost – including setup and holding costs.
This is important in industries where production is done in batches.
For investors/traders, understanding a company’s EBQ can help understand its production efficiency and cost management.
Efficient EBQ management can indicate a company’s capability to optimize production schedules and inventory levels.
Conclusion
Studying inventory optimization helps in understanding a company’s operational efficiency, cost management, and responsiveness to market dynamics.
Companies that excel in inventory optimization (where such is important) often demonstrate superior financial performance and risk management.